【解构智能工厂】系列之行业篇:成就“锂”想——和利时锂电正极材料行业综合解决方案
发布时间:2024-09-30 00:47分类: 无 浏览:442评论:0
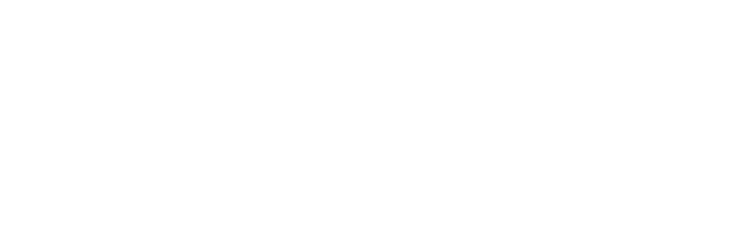
在数字化转型的浪潮中,智能工厂成为企业追求高效、智能、绿色、可持续发展的重要途径。本系列专栏“解构智能工厂”旨在深入探讨智能工厂的架构与实现路径,依托和利时Hiaplant数智化转型平台,揭示“智能化成就卓越”的奥秘。本篇文章摘选行业成功实施案例,聚焦行业特点及实际用户需求,形成面向锂电正极材料行业的综合解决方案,供您参考。
建设方案背景
随着锂电池市场的快速增长,对于锂电池行业而言,提升生产效率、优化产品质量、确保生产安全环保已成为企业发展的重要课题。通过建设智能工厂,能够满足市场对锂电池产品的快速变化需求,提高企业核心竞争力。本方案旨在为锂电池行业提供一套全面的智能工厂建设方案,涵盖设备自动化、生产智能化、数据集成化、物流智能化、质量追溯化、安全环保监控、人才培训和技术支持以及持续改进和创新等方面。
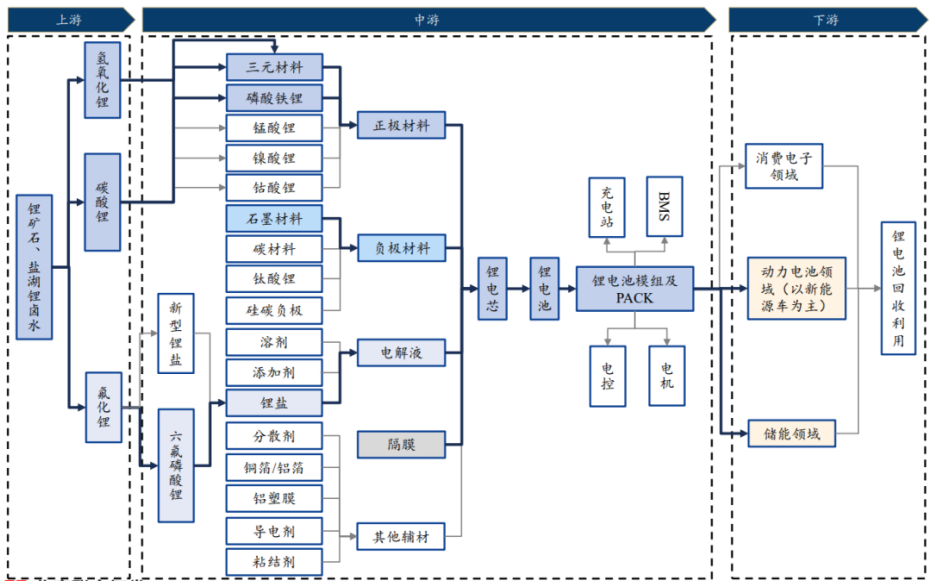
锂电池材料产业链的上游主要是原材料供应商,包括金属原材料、化工原材料、辅助材料等;中游为锂电池材料制造商,主要包括正极材料制造商、负极材料制造商、电解液和隔膜制造商等;下游为锂电池,主要应用于新能源汽车、储能系统、消费电子等。其中,新能源汽车是锂电池最大的应用领域。
建设方案分阶段实施
不同用户企业面临着不同的挑战,优先级也不是一概而论,因此智能工厂建设方案也需因企而异。根据企业的实际情况,分阶段部署。
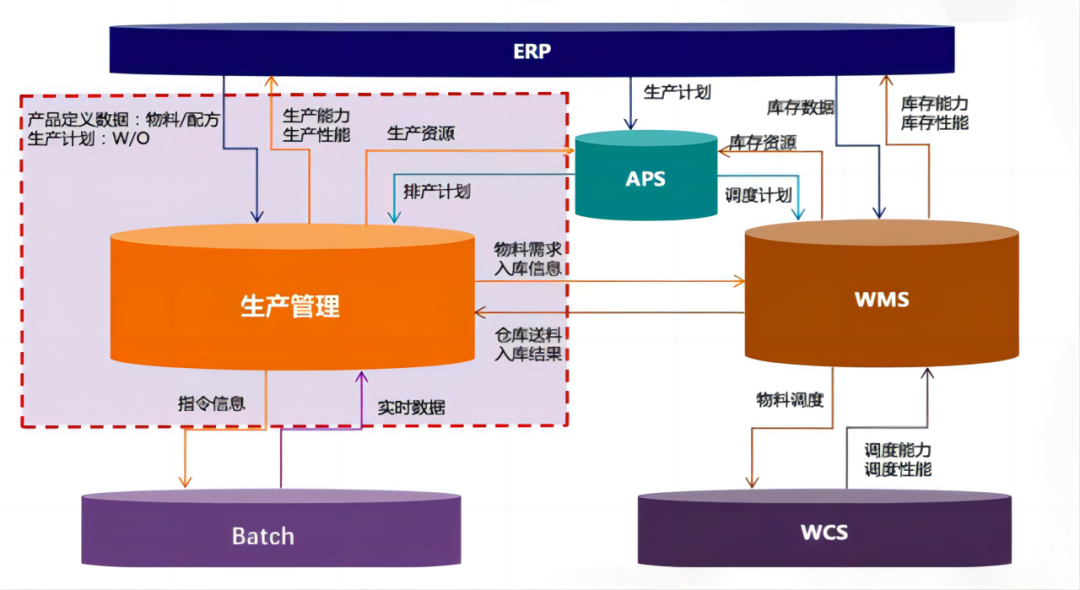
图/锂电正极材料行业解决方案架构图
阶段1丨企业诊断与分析
评估企业自动化与信息化现状,明确管理改进方向,识别智能工厂关键系统支撑点与业务需求。
阶段2丨顶层设计与目标制定
基于现状分析,构建完整的顶层设计,完成近远期的智能工厂实现目标制定,设计数字化赋能场景,构建智能工厂运行基础的技术架构与保障体系。
阶段3丨实施路径规划与管理体系建设
根据用户需求的迫切程度,确定项目的3-5年的实施路径规划, 建立完善的智能工厂管理制度与体系。
实施关键五要素
全厂自动化水平提升
全厂自动化水平的提升是基础,数字化与智能化的推进皆需以此为基础稳固前行。锂电池正极材料生产成套设备较多,均通过PLC控制,将PLC统一通讯至DCS系统,实现全流程集中控制。采用先进控制系统,提升工厂自控投用率,使之关键生产环节实现基于模型的先进控制和在线优化。
基础设施智能化需求
随着科技的飞速发展,工厂基础设施的智能化已成为制造业转型升级的关键。通过整合先进的信息技术、自动化技术和人工智能,工厂基础设施的智能化不仅提高了生产效率,还为企业的可持续发展奠定了坚实基础。基于行业的现状,基础设施的智能化建设方面,我们主要关注以下一些方面:
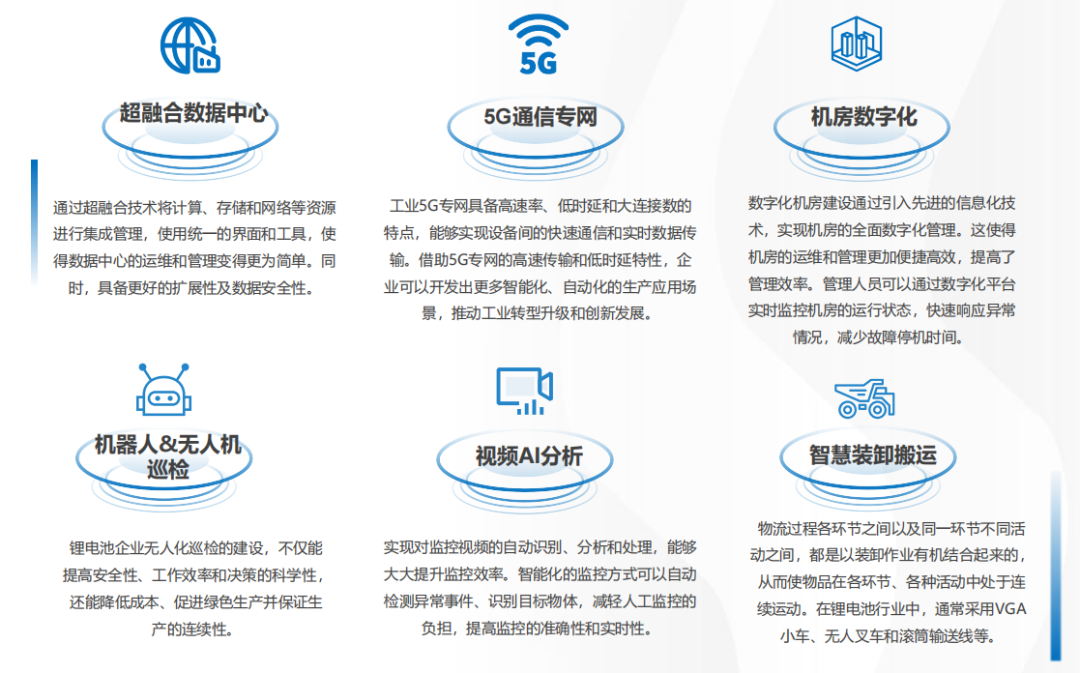

超融合数据中心:将计算、存储和网络等资源进行集成管理,使数据中心的运维和管理变得更简单,同时具备更好的扩展性及数据安全性。

5G通信专网:工业5G专网具备高速率、低时延和大连接数的特点,能够实现设备间的高速传输和低时延。

机房数字化:机房的运维和管理更加便捷高效,管理人员可实时监控机房运行状态,快速响应异常情况,减少故障停机时间,提高管理效率。

机器人&无人机巡检:提高安全性、工作效率和决策的科学性,保证生产的连续性。

视频AI分析:对监控视频的自动识别、分析和处理,减轻人工监控的负担,提高准确性和实时性。

智慧装卸搬运:在锂电池行业中,通常采用VGA小车、无人叉车和滚筒输送线等。
数据标准化与协同
各项技术与解决方案的优先级同样需要根据企业的实际需求和迫切程度灵活调整,确保资源的合理配置与高效利用。建议企业在智能工厂的顶层设计期间,重点关注两大核心问题:一是数据的标准化,确保数据统一,实现企业数字化转型,为智能应用奠定基础;二是实现数据协同与互联互通,即信息系统的全面集成,打破信息孤岛,促进各部门、各系统间的数据流无缝对接与高效协作。
生产执行智能化(Batch批量控制系统)
锂电池正极材料生产成套设备较多,均通过PLC控制,很难实现较高的自动化,导致现场操作固化,单步人工操作等方式来混料、干燥、烧结、温控等,既增加人员的操作强度,也对员工素质提出了更高要求,即使这样,其操作出错率并未降低,且控制的稳定性不足,致使品质不易稳定,生产的隐性成本较高;同时,常规DCS系统,不能较灵活地应对不同批次工艺条件、参数等变化。
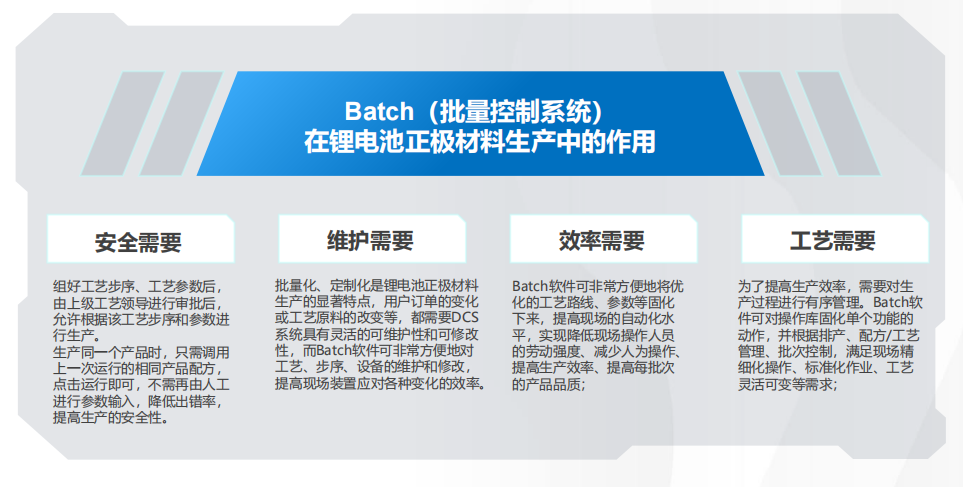
如何对锂电池生产过程进行精细化控制、管理,并实现对生产全流程的监控,是目前大部分企业的困惑,如何解决这些生产过程的束缚,让生产企业有更多精力投入到工艺创新、产品创新等主业上,和利时自2003年开始专注于间歇生产行业的自动控制,在2005年率先采用独立批量控制软件Batch1.0进行生产控制和管理,并采用ISA-S88,ISA-S95等国际标准,在2010年推出了批量控制软件Batch,通过Batch(批量控制系统)实施,给锂电池正极材料企业生产过程控制带来以下几个方面的进步:
01
五清:批次清、数量清、质量清、责任清、生产动态清
02
四分批:分批入料、分批加工(反应)、分批输送、分批入库
03
二快:产品质量波动原因查找快、新产品新配方投产周期快
04
二保密:配方保密、生产工序保密
实施效果展示
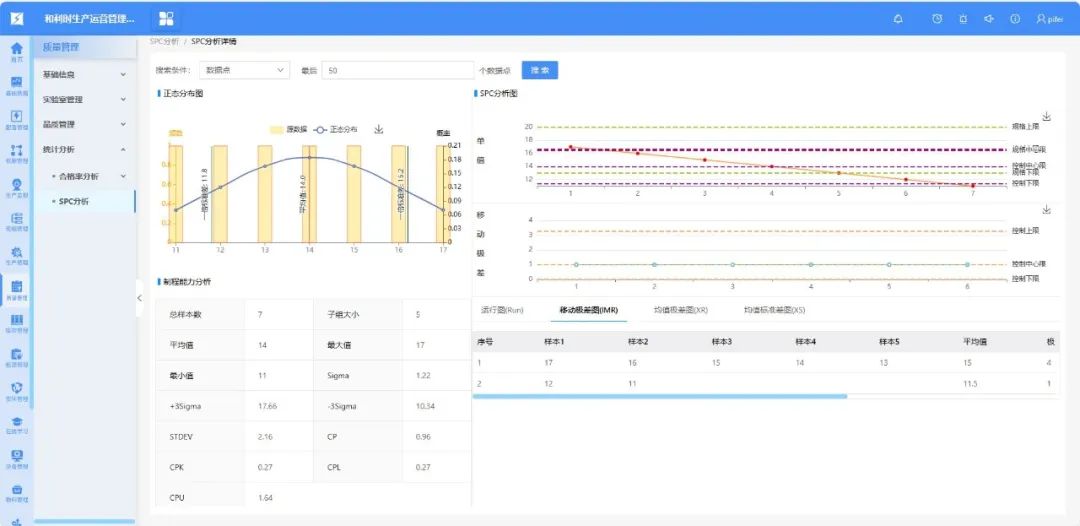
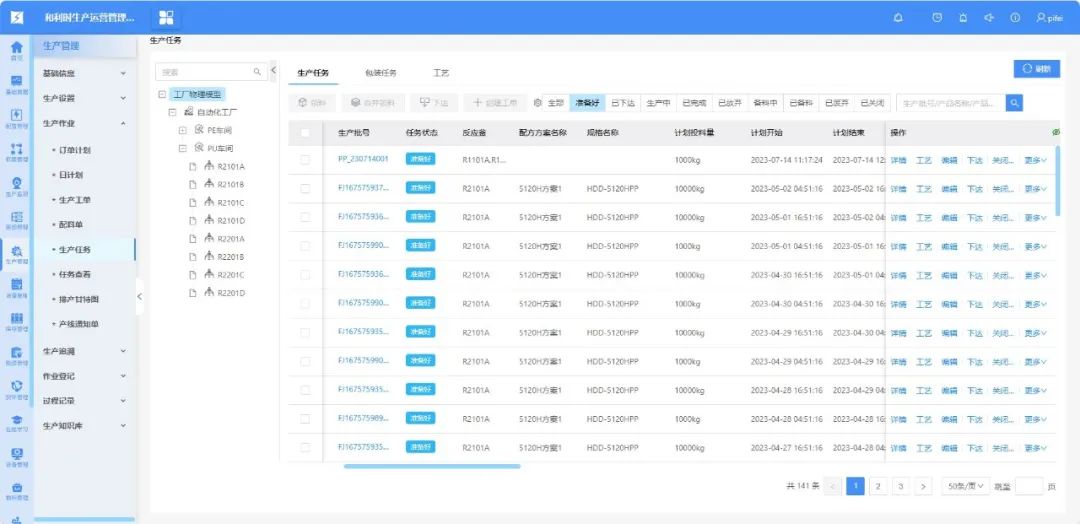

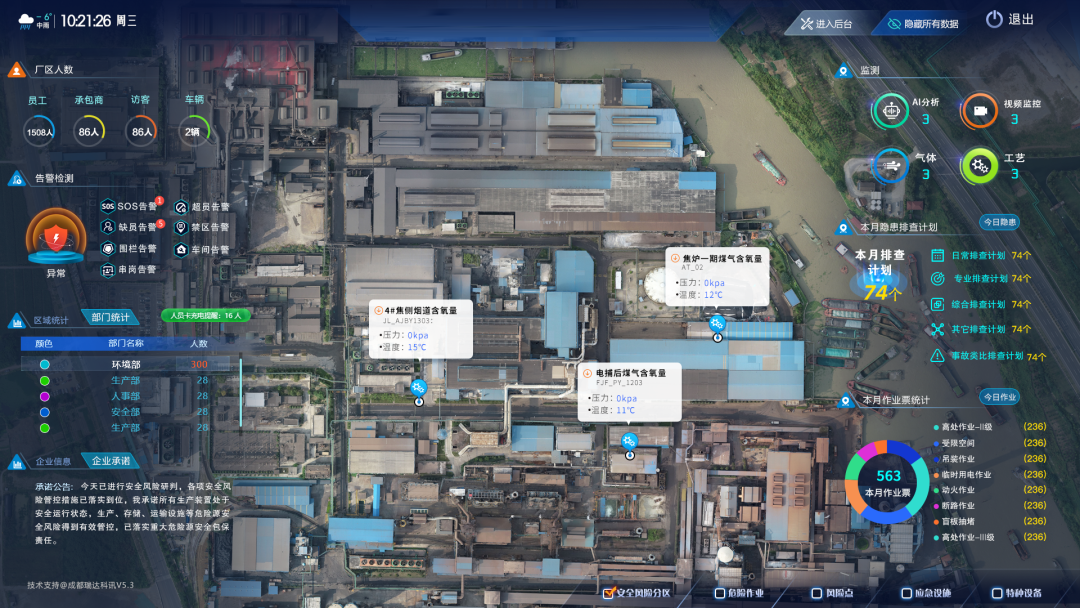
在【解构智能工厂】系列专栏的后续篇章中,我们将继续深入剖析智能工厂的各个层面,揭示更多数智化转型的奥秘,期待与您一同见证智能制造时代的辉煌。
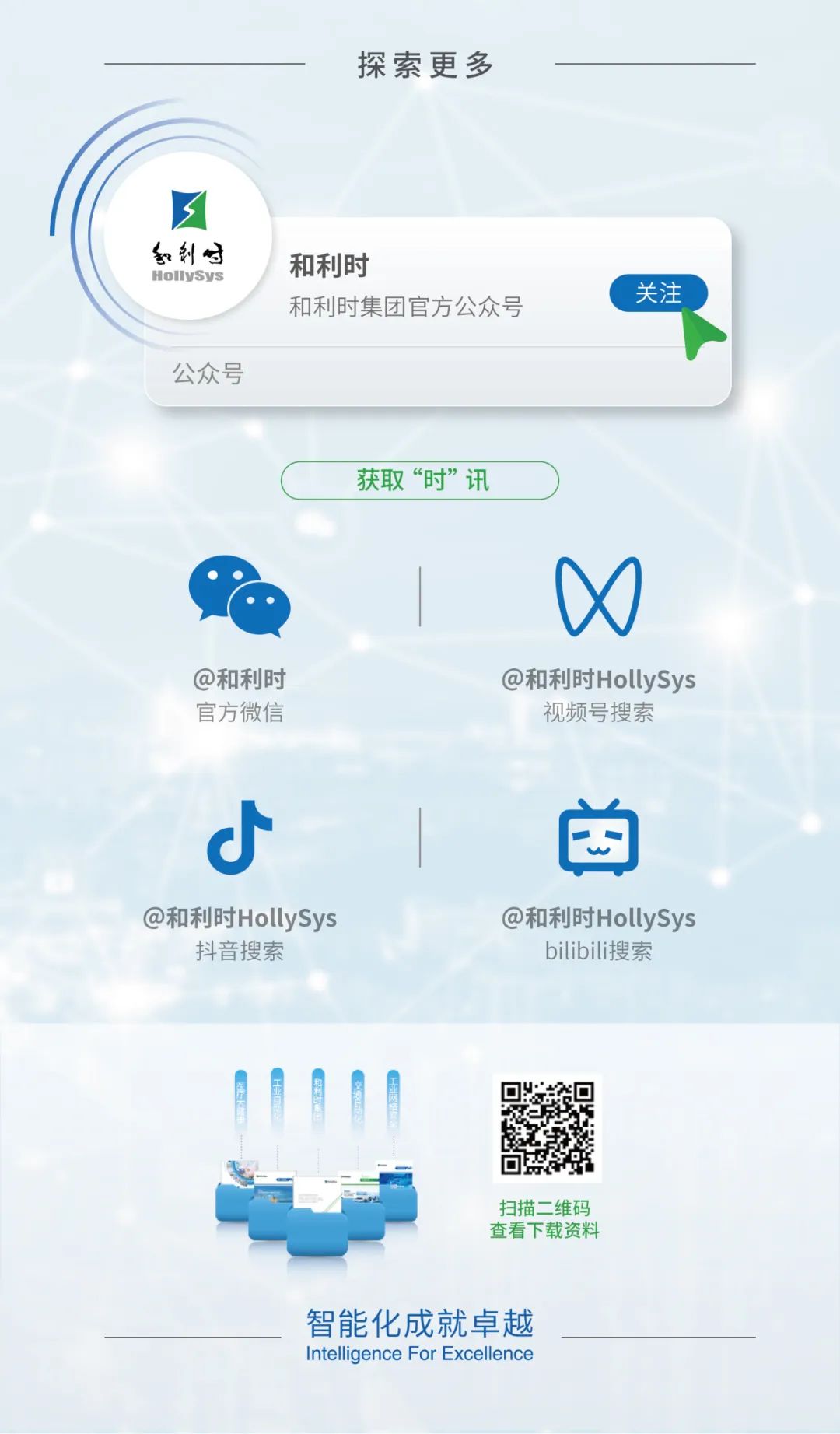
相关文章
- 交控科技董事长郜春海:低空经济需场景应用驱动,规则制定和基础建设刻不容缓
- 卡特彼勒为中航云南沙数据中心提供电力保障
- 喜报 | 金地空间科技、安承电梯荣获2024中国物业服务企业500强优选服务商
- 追光者成光,先进风采照亮前行之路
- 智启新机 云创未来|紫光云位居2024年IDC MarketScape中国容器平台厂商评估领导者象限
- 印度尼西亚政府代表团一行莅临朗新科技集团参观交流
- 远光智能问数:解锁数据价值,洞察业务先机
- 【邀您共赴】和利时闪耀2025工控网年会!硬核科技+实力奖项!
- 中科创达荣获小米 SU7 & SU7 Ultra 首批 “梦想赞助商”
- 智汇长安,赋能未来——和利时西安培训中心正式启动,开启工业智能化人才培养新篇章
- 排行