全员推精益 | 装备产业发展中心102车间:解锁效率革命
发布时间:2025-04-28 04:00分类: 社会 浏览:144评论:0
导读:编者按当前,公司党委正在全面深入推行精益管理。即日起,微信公众号开设“全员推精益”栏目,刊登各单位在精益管理方面提炼出的好方法与举措,一起分享交流学习。装备产业发展中心102车间在...
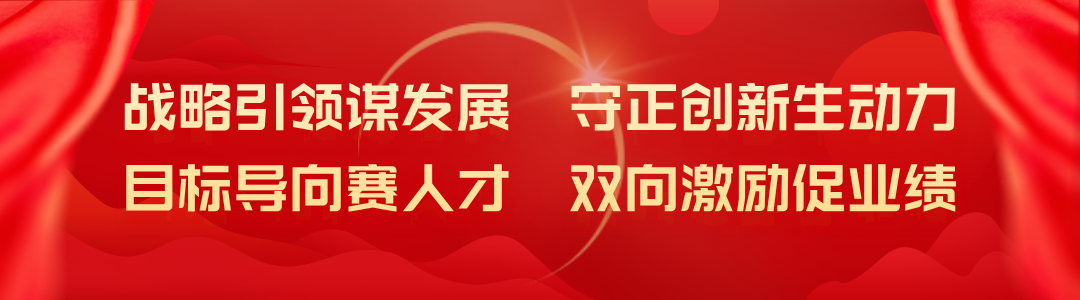
编者按
当前,公司党委正在全面深入推行精益管理。即日起,微信公众号开设“全员推精益”栏目,刊登各单位在精益管理方面提炼出的好方法与举措,一起分享交流学习。
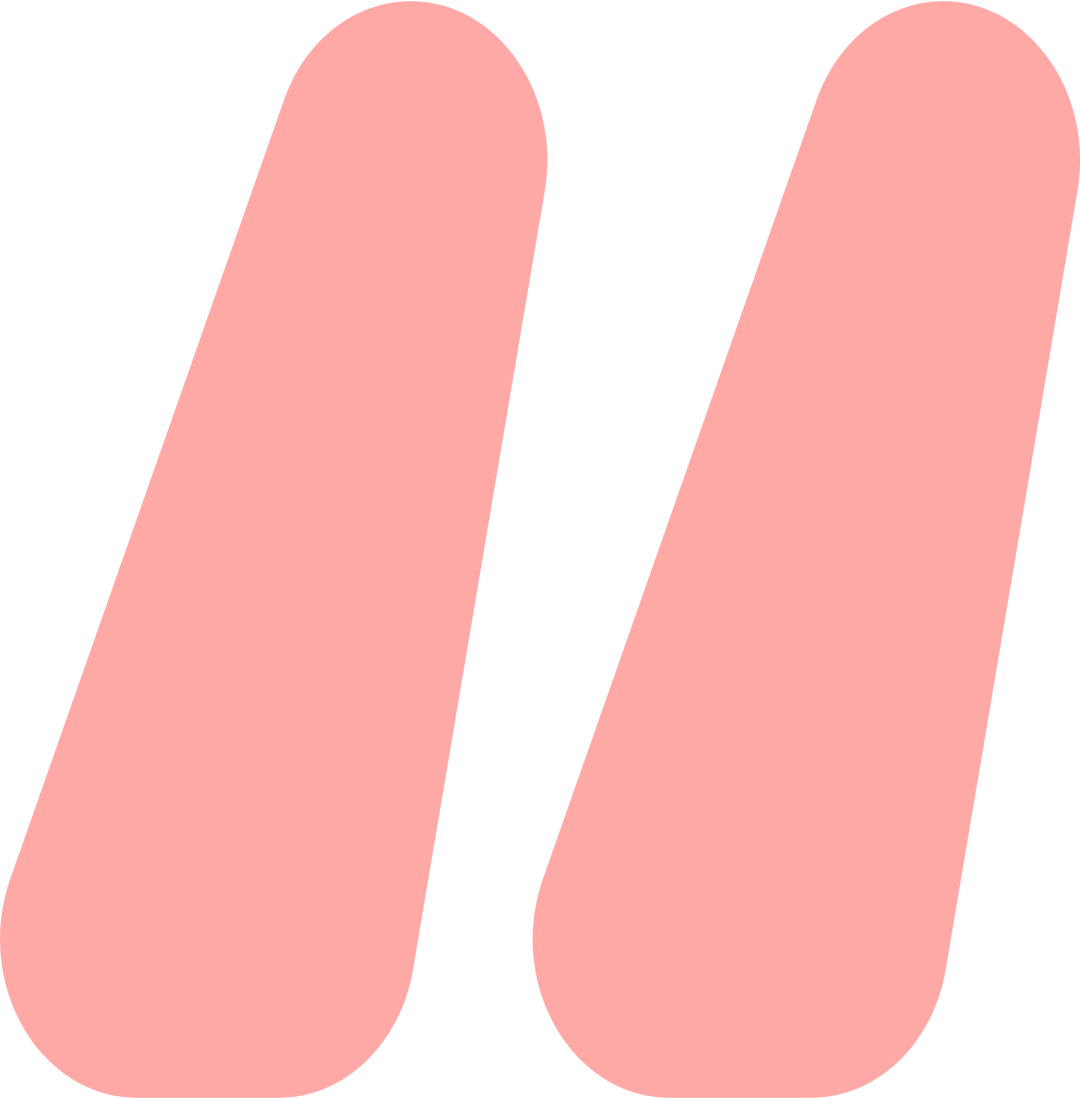
装备产业发展中心102车间
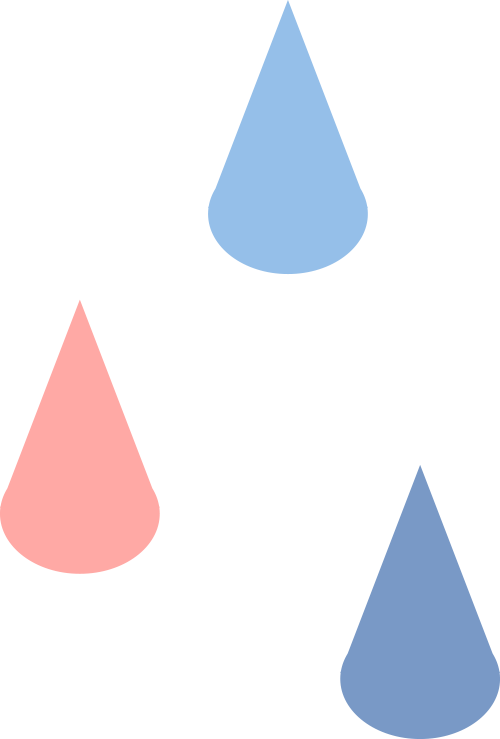
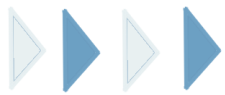
破局传统
从单件到多件的技术跃迁
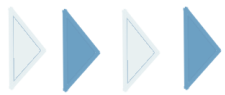
传统加工模式中,单件装夹导致设备频繁启停、员工重复操作,既制约产能又加剧疲劳。“彭弘首席技师工作室”和车间技术组聚焦痛点,通过优化工装夹具设计和产品下料方式,将多个工件集成于同一夹具,配合数控程序升级,实现单次装夹同时加工5件产品。
“过去加工一个零件需要装夹2分钟,现在一次装夹完成5件,设备纯切削时间的总体占比从60%提升至 80%。”数控一组班组长赵亮指着正在运行的加工中心介绍道。
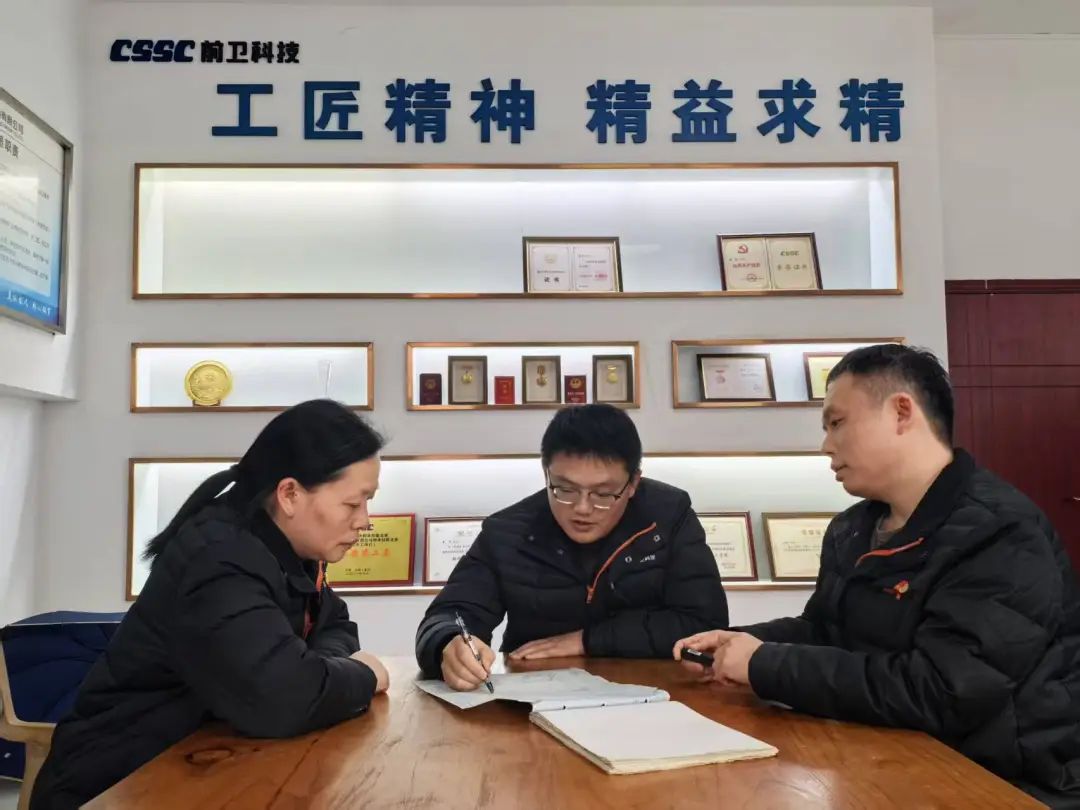
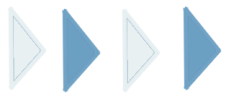
降本增效
释放设备与人力的双重潜能
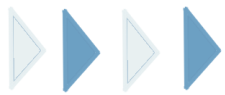
新的加工模式不仅让设备“少停机、多干活”,更重构了生产组织逻辑。通过成组加工与程序模块化设计,员工可有效操作2~3台设备,人均效能提升40%。
员工朱程军感慨:“以前每25分钟就要重新装夹,现在设备连续加工25小时不间断,甚至通过再次集成可以达到一次装夹连续加工7.5~12.5小时不间断,我们会有更多时间进行质量自检和技能学习。”
本次革新并非是孤立的技术尝试,更是车间“精益管理”的重要一环,这不仅是加工方式的改变,更是生产思维的进化。接下来,车间将持续深耕工艺创新,让“效率革命”的火种点燃高质量发展新引擎。
通讯员:贺尧(装备产业发展中心)
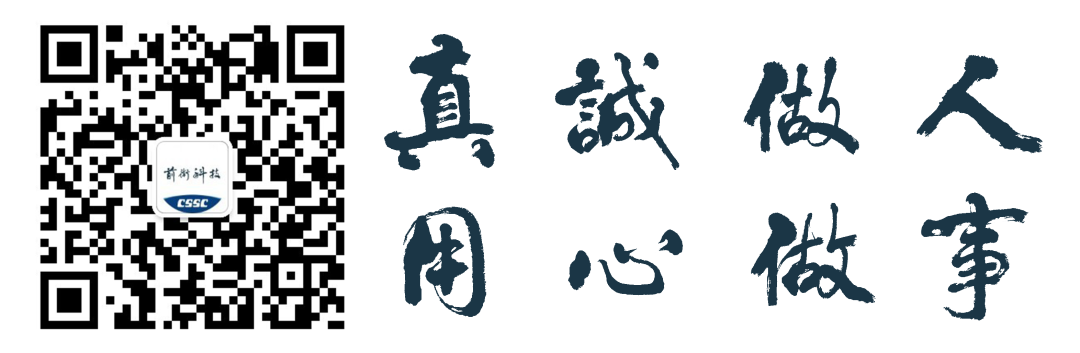