2025 March Issue | MINTH MBU Light Chaser NO.21
发布时间:2025-04-14 23:46分类: 无 浏览:248评论:0
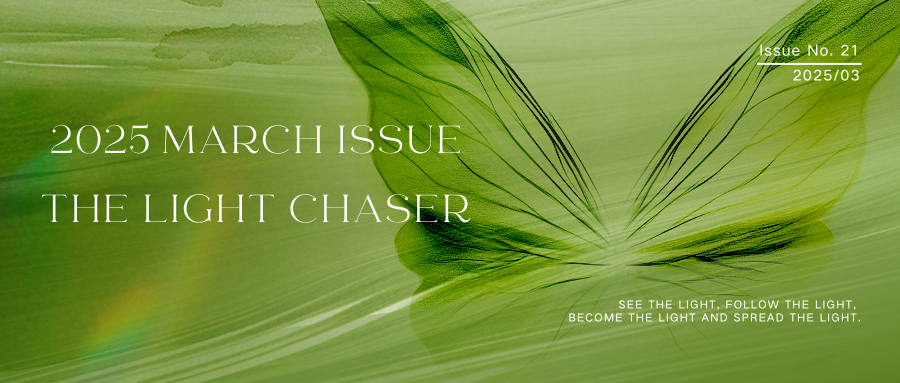
-ZHUIGUANGZHE-
01.Safety Sentinel At All Costs
<
02. Cracking It With Truth And Courage
<
03. Crossing From 20 Lines To 22 Lines
<
01.
「Safety Sentinel At All Costs 」
Tianjin Shintai-Cui Chunlong
1
In the dimly lit warehouse aisles during the wee hours of the morning, safety officer Cui Chunlong was conducting an on-site patrol when he spotted a storekeeper driving a tow truck by, with the safety belt dangling empty from the driver's seat and failing to honk as required at the intersection. "Stop the vehicle!" Cui Chunlong halted the truck, to which the storekeeper hastily explained, "This shipment needs to be out in a hurry..." His words were cut short as Cui interrupted, "Haven't there been enough accident reports of drivers being ejected from their cabs for not wearing seat belts? Who can afford to take that responsibility?" After saying this, Cui Chunlong deducted safety assessment points from the department as per regulations.
Moments like this, where he "offends people," are a constant in Cui Chunlong's work. Last month, while reviewing surveillance footage, Cui Chunlong discovered a supplier violating regulations by bringing a lighter into the factory and smoking outside designated times. He promptly contacted the supplier's supervisor, who insisted repeatedly, "I definitely didn't bring a lighter, and I didn't smoke!" Cui Chunlong didn't say much in response, merely informing the other party that if any violations were indeed found, the maximum penalty would be imposed and asking if they agreed. After both sides reached a consensus, Cui Chunlong sent over the footage of the smoking incident. Upon seeing the video, the supplier attempted to seek leniency and wanted to add Cui Chunlong on WeChat for private negotiations. However, Cui Chunlong firmly refused and insisted on imposing the agreed-upon maximum penalty.
Gradually, changes were taking place due to such persistence: fewer people were bringing lighters into the factory, hardly anyone wore Bluetooth headphones outside break times, and supplier management became increasingly standardized.
"Everyone thinks I'm making a mountain out of a molehill, but if one day they suddenly praise me for being amiable, that's when we should really be worried," Cui Chunlong always held onto this courage to "offend people." This courage stemmed from the company's 23 safety bans and red lines, regulations that allowed for no negotiation.
Integrity is adhering to principles even when knowing it will offend others; honesty is the unwavering bottom line when faced with temptation, the one who says "it must be done" among thousands of "it's not necessary." Every time Cui Chunlong stuck to his bottom line, he added weight to the word "safety" – a shield of life forged from countless instances of "no compromise," a lonely yet steadfast watch in the dead of night.
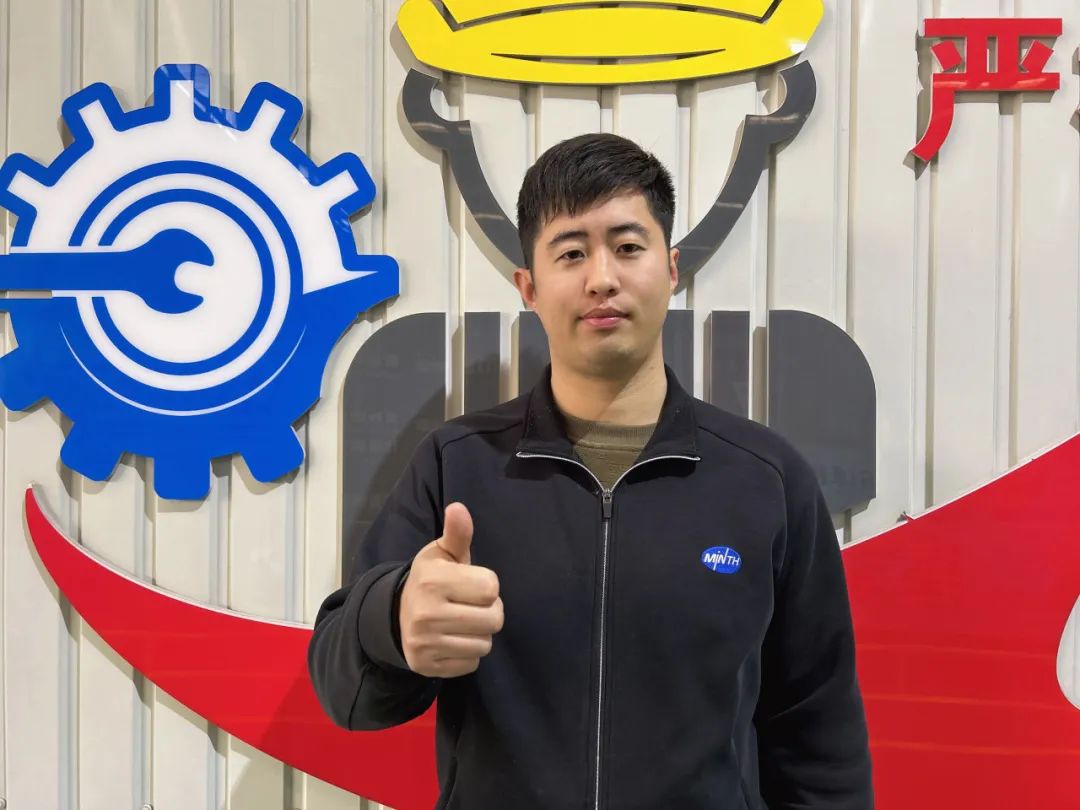
02.
「 Cracking It With Truth And Courage 」
Changchun Minth-Zhang Linjian
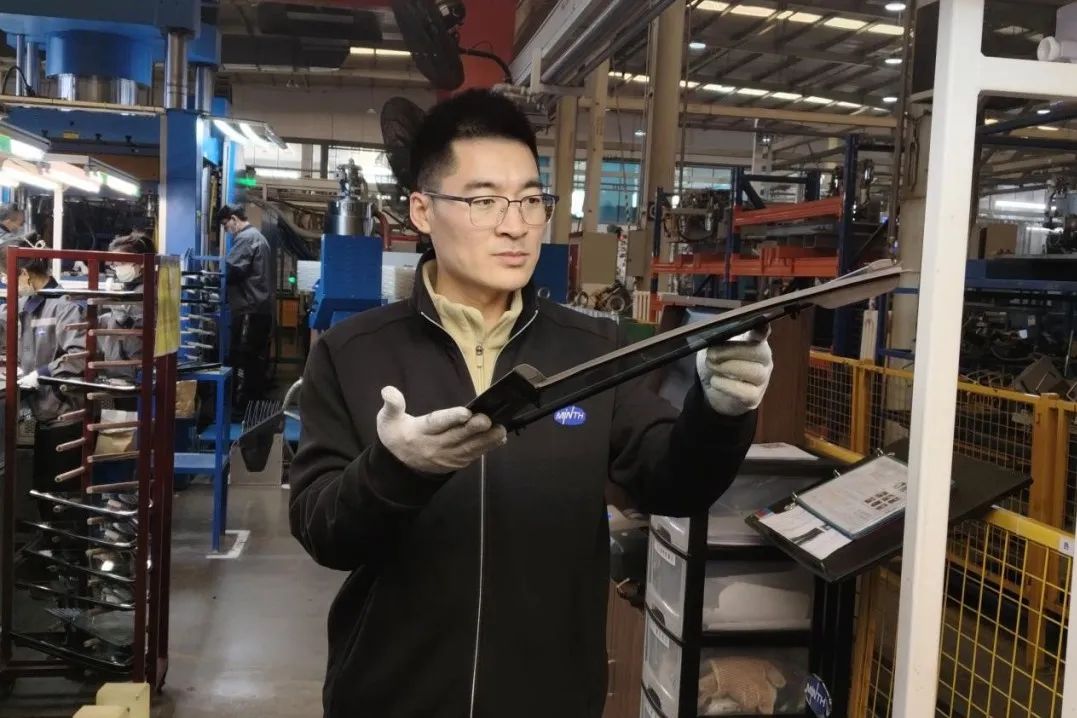
Early one morning in September 2024, quality engineer Zhang Linjian stands at the left injection moulding line of the VW 491 triangular window with a frown on his face. He is faced with a thorny problem: a bulge has reappeared in the fixed position of the injection moulded product. The solution to the problem is not only related to production efficiency, but also to the confidence of the team and the trust of the customers.
He took a deep breath and gently tapped the surface of the machine with his fingers, as if thinking of something. First, he carried out a detailed analysis with the pre-project, production and process teams, and initially judged that the parts supplied by the supplier were not flat enough, leading to an unstable injection status. He then asked the supplier to review the fittings, arranged for grinding and pushed for a change to reduce the height of the rib. This series of measures seemed to be implemented in an orderly fashion and the failure rate of the production line was reduced. However, the problem was not completely solved and the line still had problems.
Zhang Linjian realised that his initial analysis might have been wrong. He was faced with a difficult choice: should he continue to improve the parts along the original line of thinking, or should he re-examine the root cause of the problem? As an experienced quality engineer, he knew that continuing to take the bull by the horns would make the problem even more complicated. But he plucked up courage and decided to revisit the problem. He re-analysed the relative positions of the bright bars, fittings, glass and injection moulds. By obtaining the surrounding moulds from the previous project and re-measuring the dimensions and relative positions of the accessories, he found that the dimensional status was also a key factor.
This discovery made Zhang Linjian both relieved and stressed, as it meant that all the previous efforts might have been in vain. However, instead of hiding it, he immediately reviewed it and shared it with the production and process teams. His tone was firm and sincere: 'Our previous thinking may have been biased, but as long as we work together, we will be able to find the real solution. His honesty and courage infected the team and everyone actively contributed insights and the problem was eventually solved.
Courage and honesty are the most important qualities when facing mistakes. Only when you are brave enough to face your mistakes and start again can you truly solve the problem and move your team and company forward.
03.
「Crossing From 20 lines To 22 lines 」
Ningbo Shintai-Fang Qiang
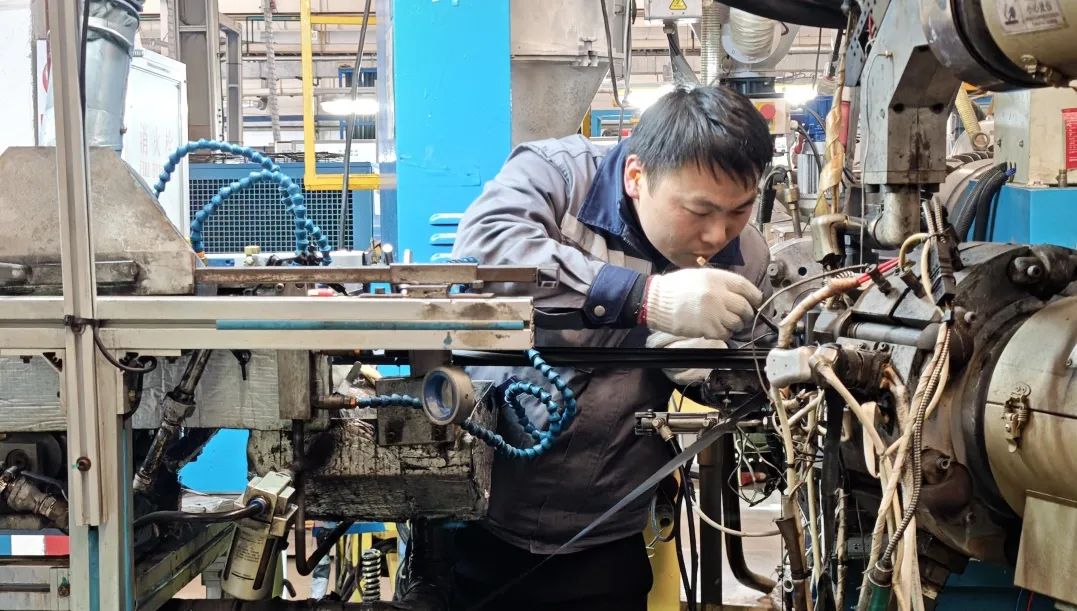
In the second half of 2024, the repositioning 22 line was faced with unprecedented challenges - orders from Geely customers surged, with a monthly demand of up to 30,000 units. In order to ensure delivery, the production line implemented a double-shift system, with a monthly load of more than 28 days. In the face of such high intensity work, every employee of the repacking line 22 felt great pressure.
At this moment, a figure stood out. He was Fang Qiang, a senior supervisor from Line 20. Although he had never been in contact with the production process of Line 22, and faced with a brand new product line and complex process requirements, he did not flinch and accepted the challenge. Fang Qiang knew in his heart that this was not only a test of personal ability, but also a heavy responsibility. Not only did he have to quickly master the operation of the new production line, but he also had to make sure that every product met the high standards of Geely's customers.
In order to adapt to the new environment as soon as possible, Fang Qiang began to study and practice day and night. He came to the workshop early every day, from the preparation of raw materials to every detail of the processing, he carefully observed and recorded. When he encountered something he didn't understand, he took the initiative to ask for advice from the old staff of line 22, and learnt the characteristics of the products and the precautions in production with an open mind. His notebook is densely filled with operation points and precautions, and he even thinks about how to optimise the process when he eats.
However, the real challenge had just begun. Geely's customers have extremely high requirements for product sections, and any minor flaws could lead to product scrapping. In order to ensure quality, Fang Qiang inspects the body set-up in the back-end process every two hours, personally checking every product. His eyes are like scanners, not sparing any details. Once he finds a problem, he always communicates with his colleagues on the production line at the first time to find a solution. Sometimes, for a subtle process improvement, he will test repeatedly until he finds the best solution.
With the efforts of Fang Qiang and his team, the product quality of Line 22 has steadily improved. With the passage of time, Fang Qiang also gradually adapted to the production rhythm of Line 22 and became more and more skilled in the operation. He not only ensured that Geely's customers' orders were delivered on time, but also won praise from them for their excellent quality.
Looking back on this experience, Fang Qiang is overwhelmed with emotion. He said, ‘This challenge made me understand more about what responsibility and accountability are. Although the process was tough, when I saw a perfect product coming off the line, I felt all the effort was worth it.’ His words are simple and unadorned, but reveal a kind of tenacity and persistence. It is this spirit that makes him not flinch in the face of difficulties, and finally delivered a satisfactory answer.
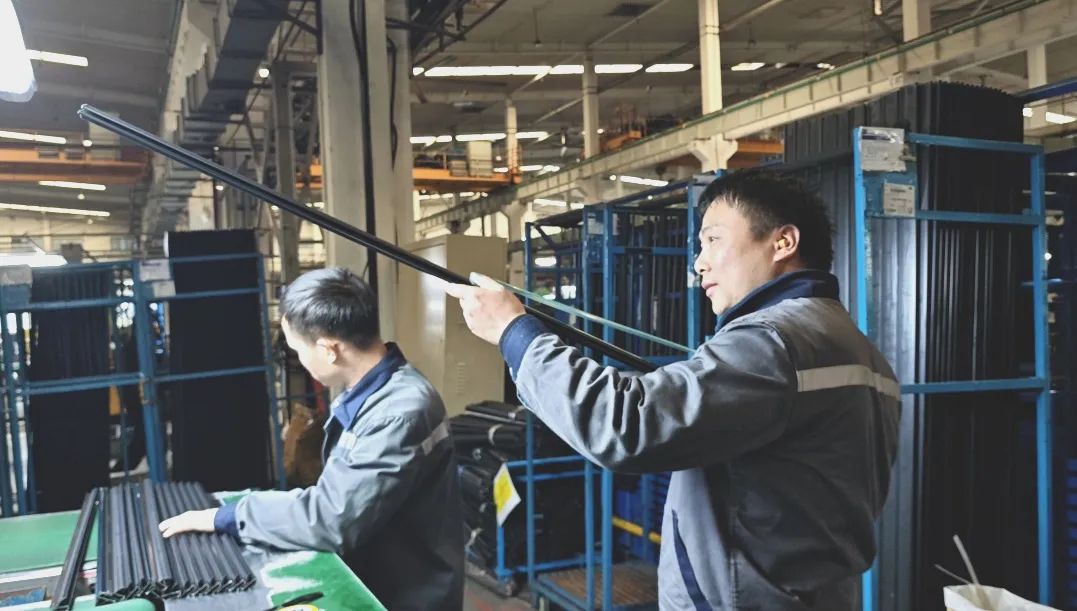
END
Light Chaser
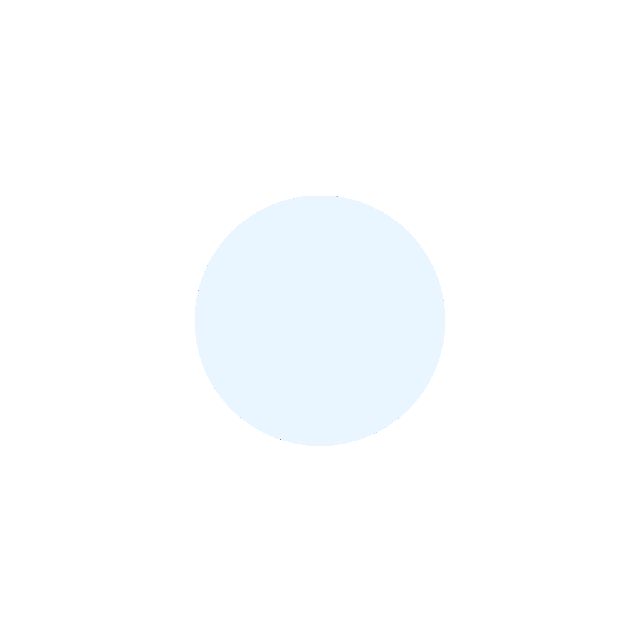
Minth MBU has created the column "Light Chasers"
Since April, 2023.
Aiming at pursuing the warm stories around us
We hope that more people will see the light, follow the light, become the light and spread the light.
- 排行